PROCESS AUTOMATION
With an easy-to-use, intelligent system, businesses can rely on automation to carry out routine daily tasks, saving time and money.
Monotonous, routine, repetitive tasks are common in the day-to-day life of a business. These tasks have low result/time ratio, and therefore can reduce the efficiency of the company undetected.
Robotic Process Automation is an advanced technical solution that makes it easy to automate office and administrative workflows. It is typically, but not exclusively, used to perform routine manual tasks such as statement generation, digital document management, filing, data capture, data transformation, email analysis, systems integration, etc.
By introducing process automation, your employees can focus on tasks that create higher added value in their daily work. This saves time and money, radically reduces the number of errors and has a positive impact on employee satisfaction.
The more time-consuming it is to manually collect data from multiple locations, the more certain that process automation is an effective solution for your business.
This automation can be implemented in any heterogeneous, isolated IT environment as a simple, fast improvement and it can be integrated with different SAP solutions and modules for process optimization.
Together with your company’s key users, we will examine the processes you want to automate, select the solutions that best fit them, plan the path to implementation and, once the development is complete, your company will reap the benefits.
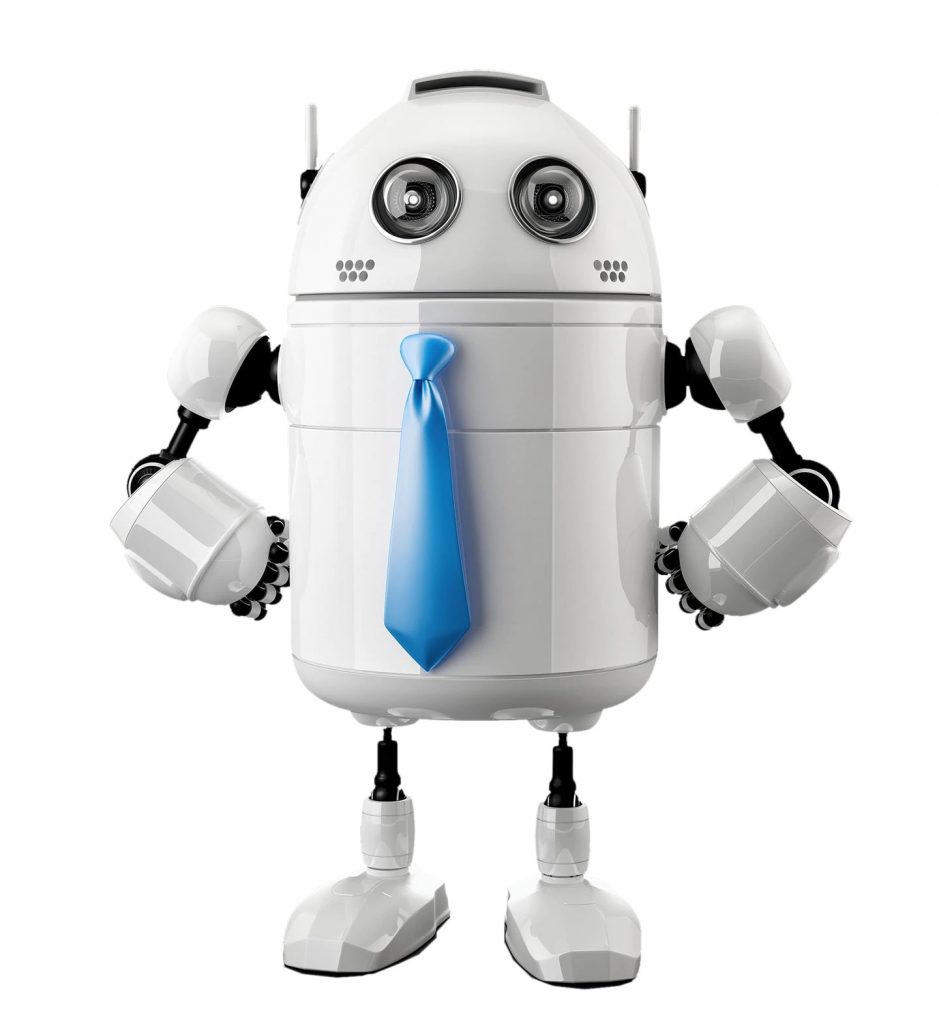
WHY AM I THE IDEAL EMPLOYEE?
- I work 7X24 hours, 168 hours per week
- I am a multi-tasker, I can do more things at the same time
- whatever they teach me, I always remember
- what I have learned, I always do perfectly
- I complete my tasks on time
- I am motivated by monotonous tasks
- I integrate easily into the team
- I'm always energetic, so I don't go on holiday
- I don't go to the doctor, but I am healthy
- I am satisfied with my salary
HOW DID WE HELP?
Download and integrate SZÉP card traffic analytics into an external system
The developed robot is installed on the client’s server, runs on a daily schedule and automatically opens the public interfaces of the SZÉP card providers available in the browser.
Using encrypted authentication stored for the robot, it enters the online interfaces and navigates to the statement menus, mimicking the user’s actions.
Here, the robot retrieves the SZÉP card turnover of the service unit concerned, starting from the date of its last run, and saves it to an Excel file.
The extracted tables are sent encrypted to a third system on a dedicated API endpoint using appropriate authentication.
No user intervention is needed at all to run the process, the robot does everything automatically.
By automating processes, the company saves an average of 2 hours per employee per day, or 40 hours per month, which is around 25% of the time and therefore cost of an administrative employee.
Automatic detection of failures
In discussions with a Hungarian-owned packaging material manufacturer, it soon became clear that the main benefit of this technology for them would be a reduction in waste. For the paper as raw material is transformed into a printed, finished box as a result of a multi-stage, high-speed and typically automated process. But sometimes there are so many boxes produced in a shift that it is not possible to check them all manually.
As a first step, our experts used on-site video footage to teach the system, within a week, what perfectly finished boxes look like and what count as rejects. When the software recognised the samples with over 90% confidence, it was successfully brought into operation at the partner.
To do this, we installed a high-speed camera at the conveyor belt, the box production endpoint, and its visual image was analysed in real time by our solution. If the system detected a crumpled, inaccurately folded or otherwise non-conforming box according to our quality criteria, it immediately alerted the operator, who stopped the conveyor and removed the defective box from the line.
The Chief Operating Officer shared that the failure rate due to material defects has been reduced to almost zero and no defective boxes was shipped to the partners.